SAMIRA1
Shunting Assistant & Monitoring Interface for Autonomous Rail Application
The first phase of the SAMIRA project was realized from 05. Sep 2019 to 04. March 2023.
Initial Situation
In transportation and logistics companies there is still a very tight personnel situation due to many vacancies. Also, shunting operations of rail vehicles are still very time-consuming and cost-intensive processes and procedures, e.g. in port logistics or in freight handling centers. This was the starting point of SAMIRA.
Nowadays, shunting operations with long shunting sections are performed as two-men operations, since the one-man operation with radio remote control is far too time-consuming and ineffective due to the associated walking times passing along the whole train when changing direction. In addition, the use of radio remote controls is not a safe operation for trains longer than 550 m in certain areas due to interferences and shortages of radio transmissions. However, for short shunting sections the radio remote control is still the standard operation.
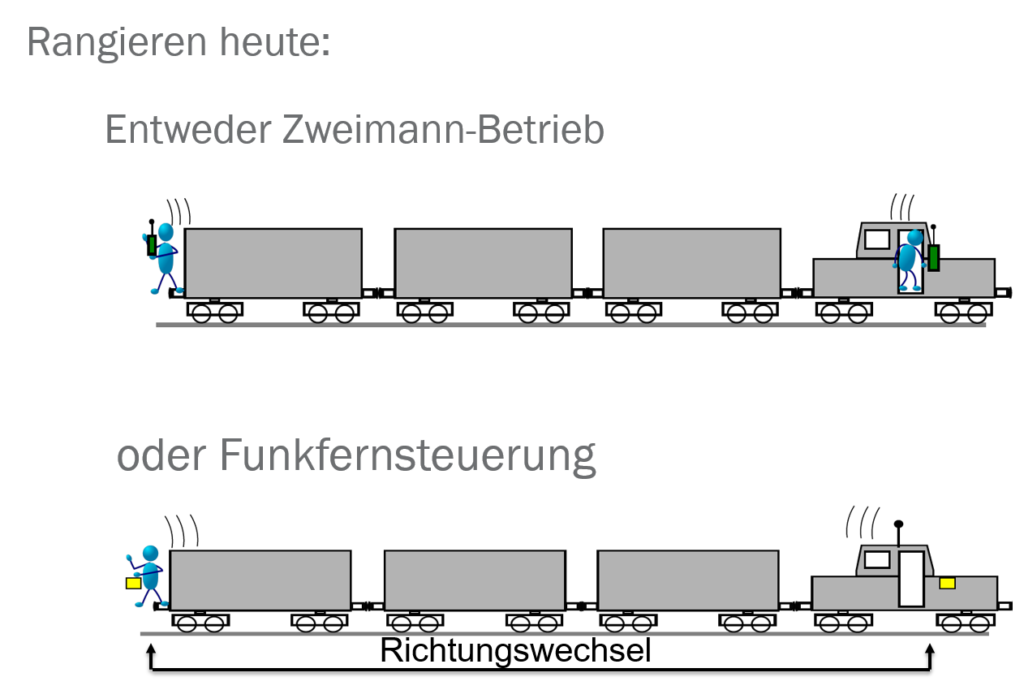
The SAMIRA-Concept
The solution to overcome these bottlenecks was resulting in the SAMIRA concept. Both ends of the train are equipped with an electronic camera and other sensors for environmental recognition, like RADAR, LiDAR, SatNav and IMU. These sensor modules (SAMIRAmobil), combined with a very secure, seamless and low-latency real-time transmission of the live images and the sensor data into the driver's cab, enables the locomotive driver (LRF) to safely steer a shunting drive “on sight” without leaving the locomotive. Both, the sensors for danger zone monitoring as well as the data transmission into the driver's cab are safety-relevant components that must meet the railway-specific requirements.
Inside the driver's cab, a touch panel as HMI (Human Machine Interface) displays a latency-free live image from the camera as well as further information, calculated data and warnings, which are projected within the video stream. By using the HMI touch panel, the LRF can also enter information about the shunting department before the train sets off, e.g. total weight, overall length, etc. This allows to calculate and provide forecasts about the current braking distance and display it within the augmented live image.
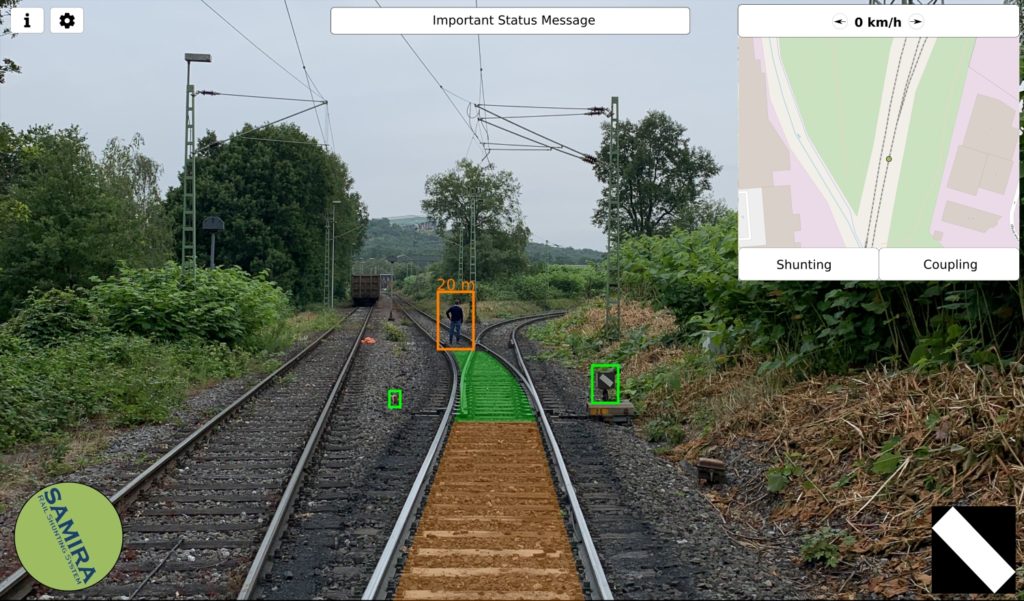
In addition to these mobile train modules, additional stationary modules for track monitoring (SAMIRAfix) increase safety on the track at blind spots. Also, an embedded RTK system enables precise positioning and thus the exact location of the train on the track.
Realization at SAMIRA1
SAMIRAmobil
Once the specifications for the overall system and the required sensors had been established, the corresponding hardware components were selected and procured and the software was developed. Then, the step-by-step implementation of the components and the subsystems led to a demonstration setup on the premises of the Reuschling company in Hattingen as depicted below. This allowed measurements and testing performed on a real railway environment at Reuschling and, together with RheinCargo, on the premises of the Prosper coking plant in Bottrop.
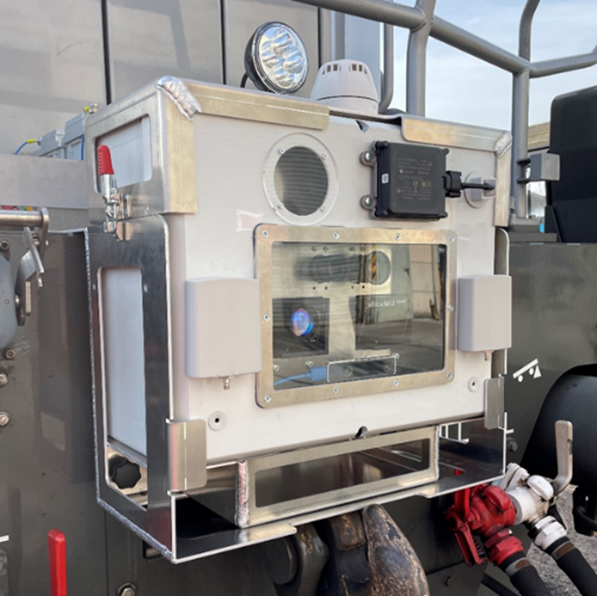
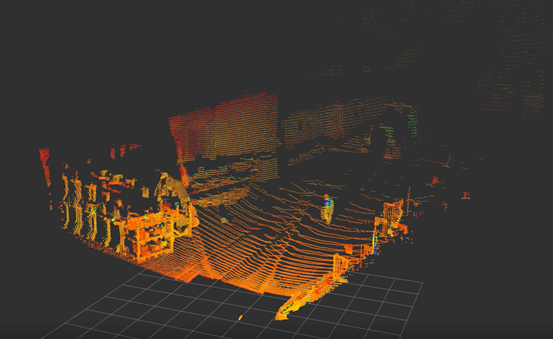
SAMIRAfix
In addition to the SAMIRAmobil device, a SAMIRAfix module was set up in parallel, too. This is used for stationary monitoring of neuralgic danger spots such as level crossings or driveways. Therefore, it is firmly attached to a building or a pole and aligned accordingly. The module contains the same hardware as SAMIRAmobil device, but does not need a RADAR sensor. It is also integrated into the wireless mesh network using the same communication interface so that the live data can be received by any authorized participant at any place in the network. So if the train driver when streams the SAMIRAfix video data on his HMI panel he gets a direct insight into a danger zone even before he reaches there with his shunting train.
The following graphic shows the setup for the SAMIRAfix demonstrator:
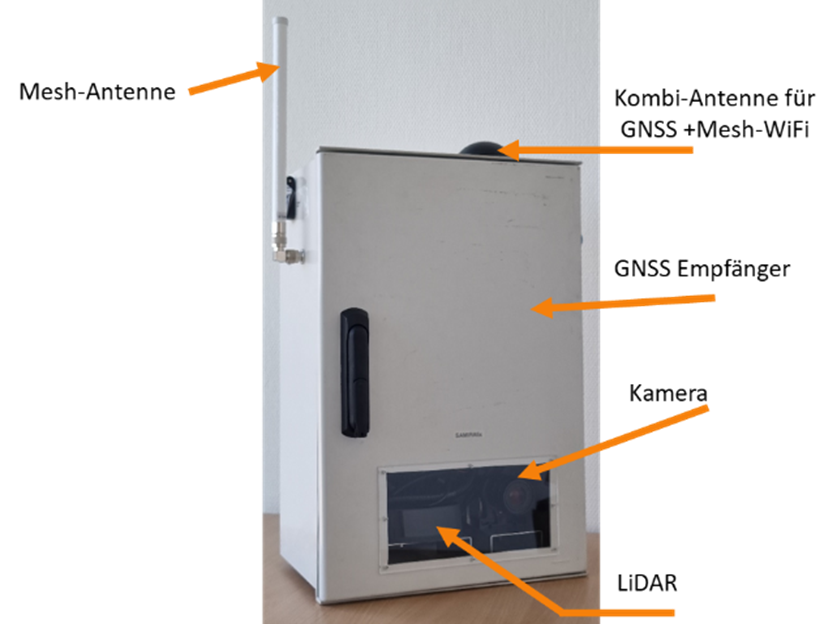
Wireless Mesh Network (WMN)
The very reliable and low-latency real-time transmission of the augmented live image from the train’s end to the driver's cab (i.e. from SAMIRAmobil to SAMIRAhmi) is essential for the acceptance of the overall system. A temporary disruption, a failure of the transmission, or even remarkable delays in the transmission timing, immediately causes a serious risk to the shunting operations. Therefore, the the network operation and the transmission channel must fulfill strong real-time requirements at any time.
For this purpose, an industrial wireless mesh network with qualified real-time data transmission and a maximum latency of 200 ms was developed and set up for SAMIRA. The runtime of the data transmissions is continuously monitored by synchronizing the system times of all network participants via the GPS signal. So each module in the entire system operates on the same time base. Each data transmission is given a corresponding time stamp so that any individual violation of the maximum latency time is immediately recognized and displayed.
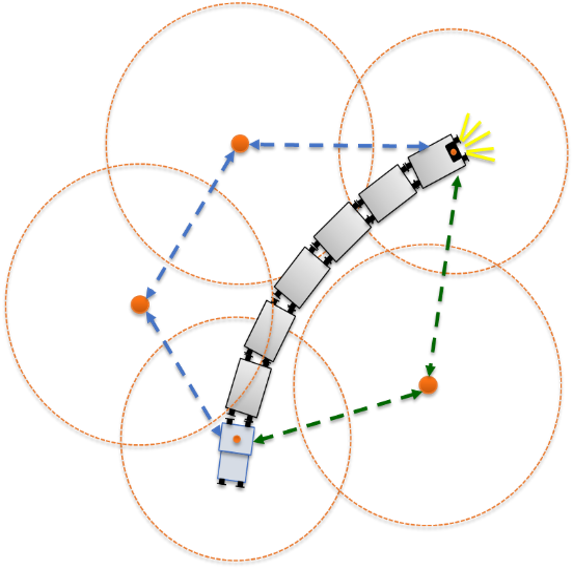
Due to the geographic extent and topographical conditions of the shunting area, several radio stations (access points) mounted with overlapping ranges are required for a consistent radio coverage. For seamless data transmission, it must be ensured that each SAMIRA station of the shunting unit always has at least one radio connection to one of the radio stations. If the shunting unit then maneuvers through the grounds, the switch of the radio connection from one radio station to the next (hand-over) must always be seamless and without data loss.
This is ensured by the controlled mesh network management, in which a seamless and loss-free hand-over of the signal from one station to the next is provided based on the current field strength profiles. If there are several transmission paths along the individual access points possible, the mesh controller always selects the optimum route. This ensures redundant transmission channels and therefore provides a fail-safe transmission system, respectively . The following figure schematically shows two possible transmission paths (green and blue transmission path). The mesh network is controlled amongst the radio stations itself and does not require a central server. This keeps the network operational even if a station fails.
Live demonstration proof of concept
At the end of phase 1 of the SAMIRA project, a very successful live demonstration of the overall SAMIRA system took place in September 2022 at the Reuschling premises in Hattingen. Also, representatives from industry took part in this day, reflecting a very positive and promising feedback on SAMIRA system. For data transmission, each SAMIRA module with its transceiver unit also represents a mesh node for communication in the data network. Additional access points were also set up, such as the Radio 4 shown in the picture below.
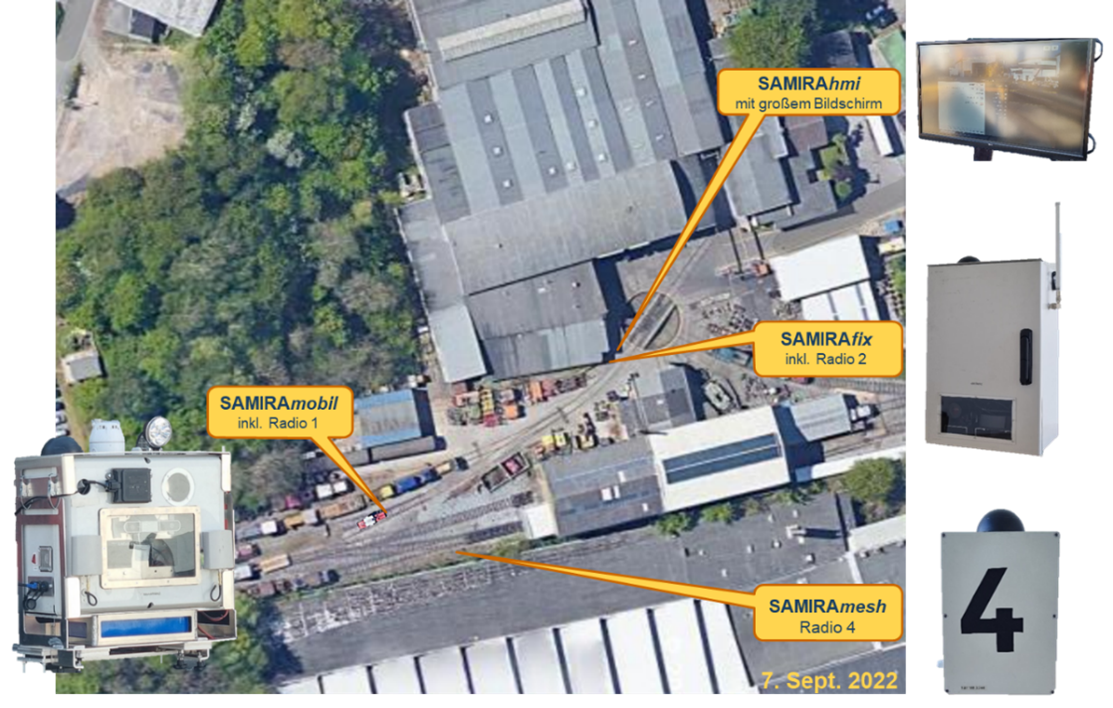
Outlook
Following the successful completion of the first phase of the SAMIRA project, the system will now undergo extended practical testing and further optimisations, focusing in particular on the following areas:
- Further development of the demonstrator system to achieve Technology Readiness Level 7 (TRL7): Demonstration of a system/process prototype in an operational environment
- Increasing the reliability and performance of object recognition in different environments by using AI
- Absolute stand-alone operation of the overall system
- Adapting to use 5G mobile communications for real-time data transmission instead of the proprietary mesh network used in phase 1
- To optimize the sensor module SAMIRAmobil in terms of size, weight and mounting options to be used in harsh industrial environments
Partners
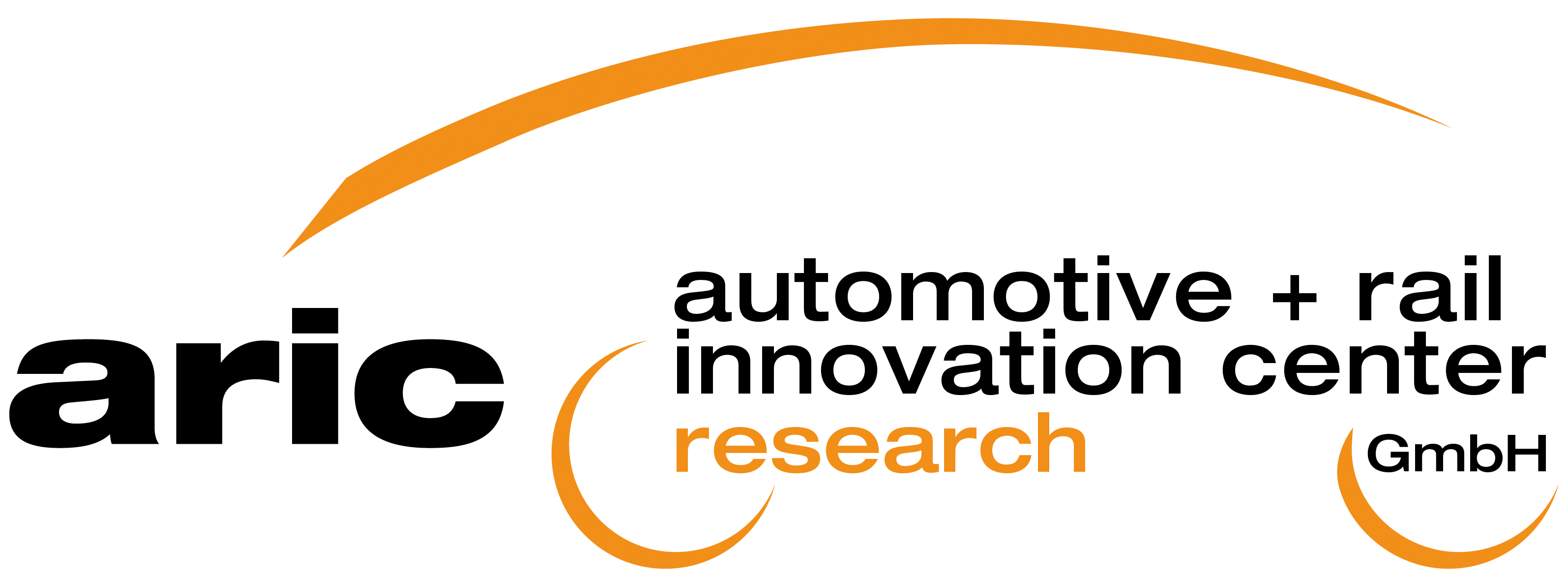
Automotive & Rail Innovation Center GmbH
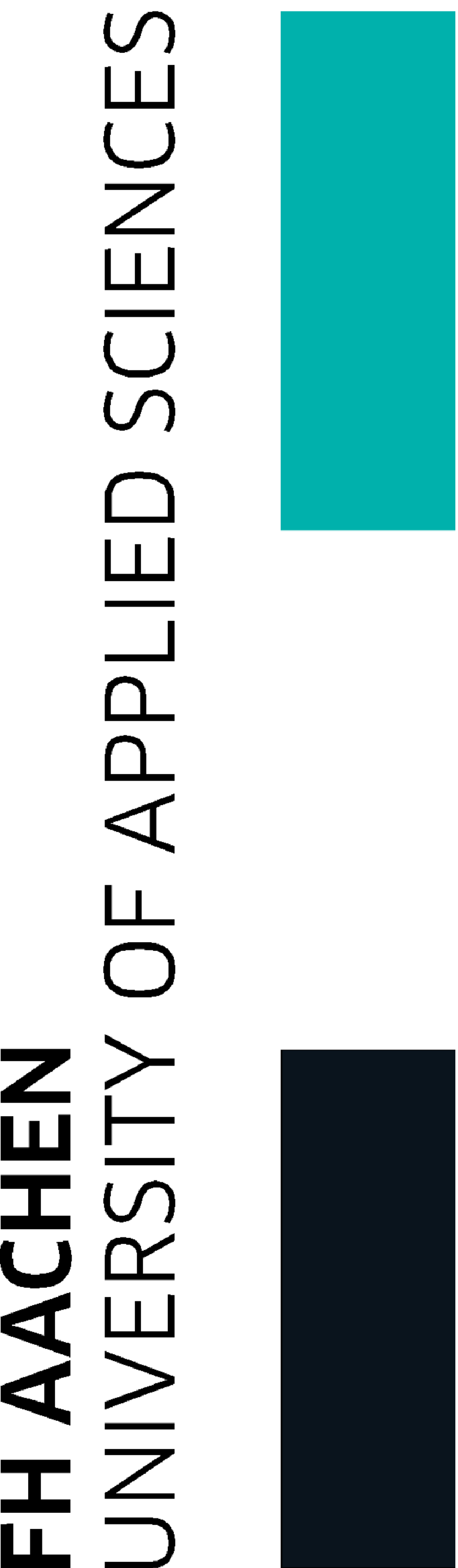
FH Aachen
Westfälische Lokomotiv-Fabrik Reuschling GmbH & Co. KG
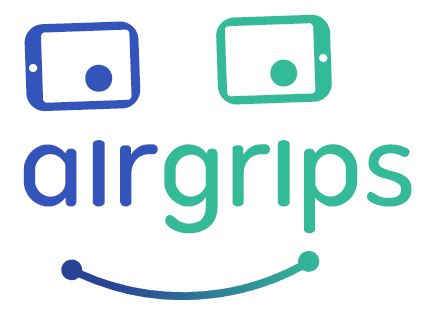
airgrips UG
Associated Partners
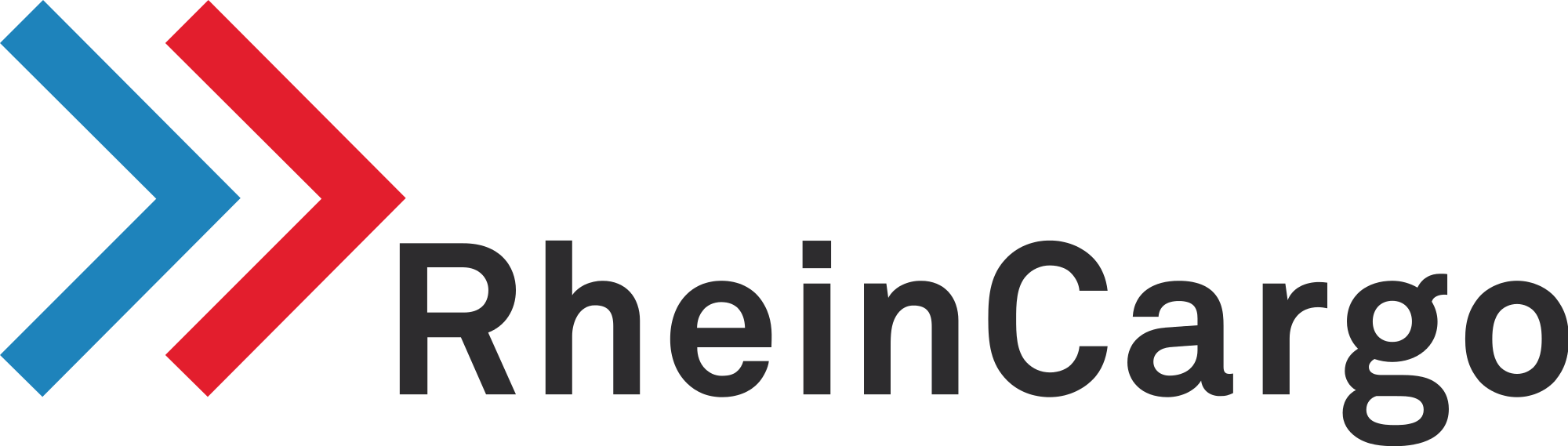
RheinCargo GmbH & Co. KG
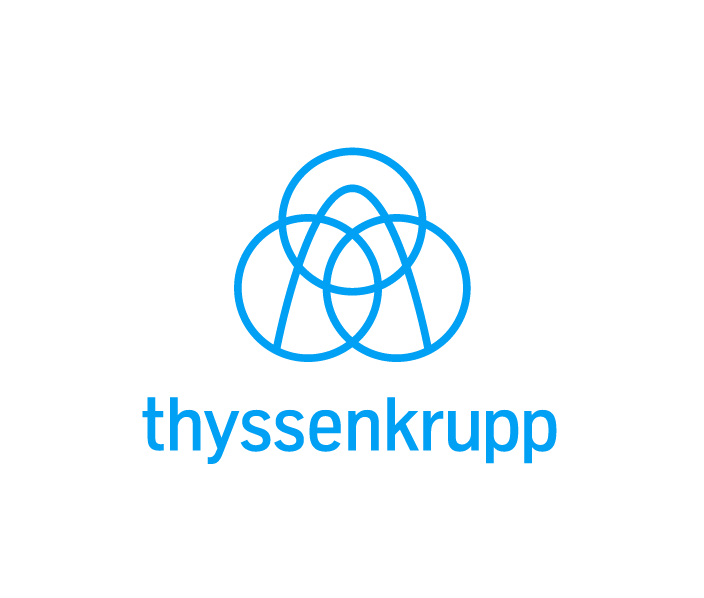
Thyssenkrupp Steel Europe AG
Acknowledgment
The entire project team would like to expressly thank the state of North Rhine-Westphalia and the European Commission for the funding received for the SAMIRA research project, without these funds the project could not have been realized.
The project was financed by a grant from the state of North Rhine-Westphalia and the European Commission with funds from the Regional Development Fund (ERDF)
Funding No.: EFRE-0801689, File No. of LeitmarktAgentur.NRW: ML-2-2-033A
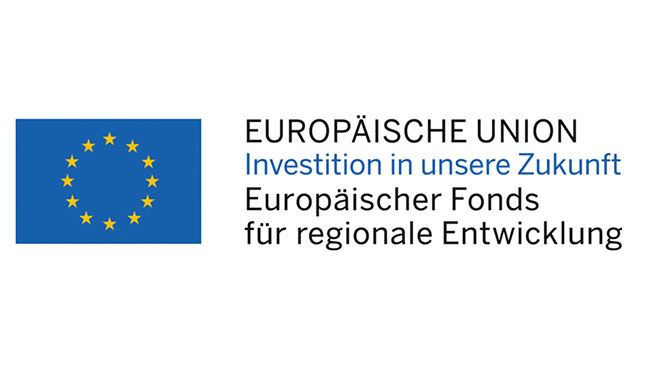
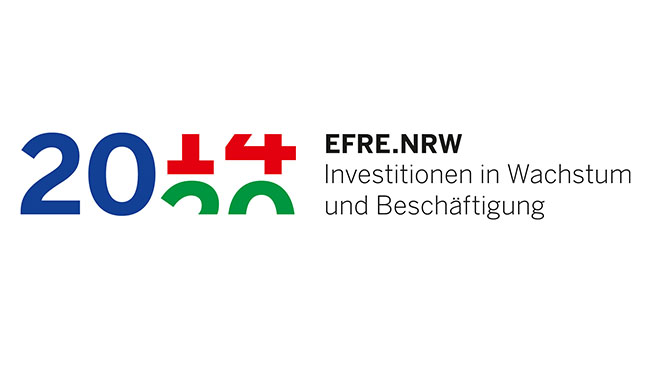
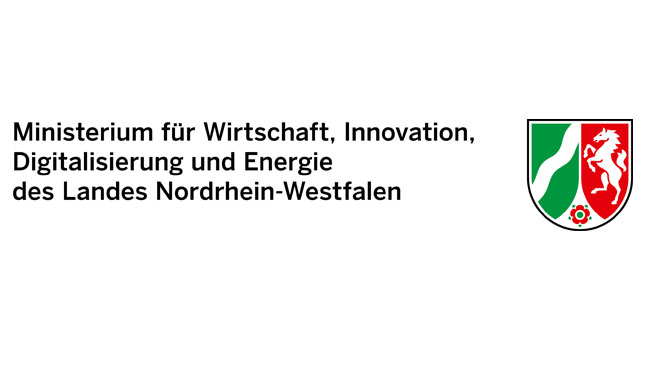